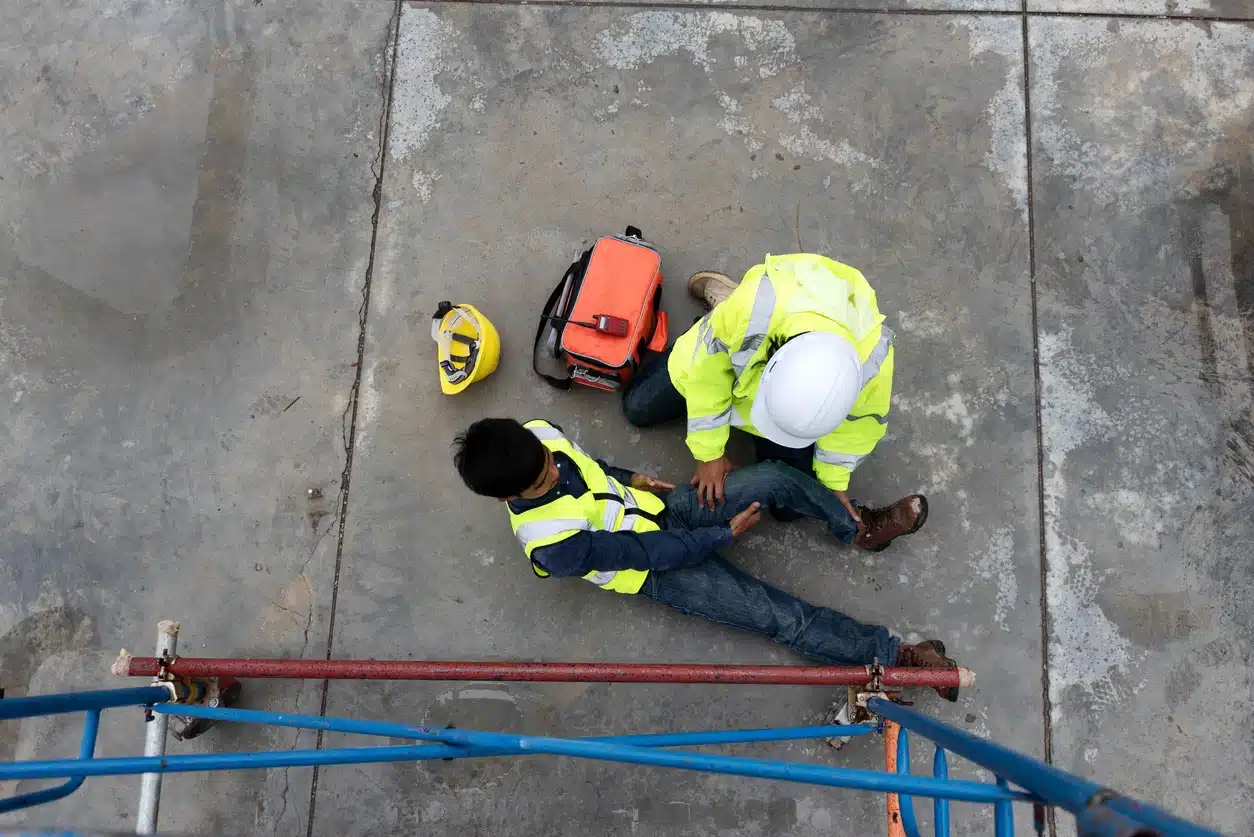
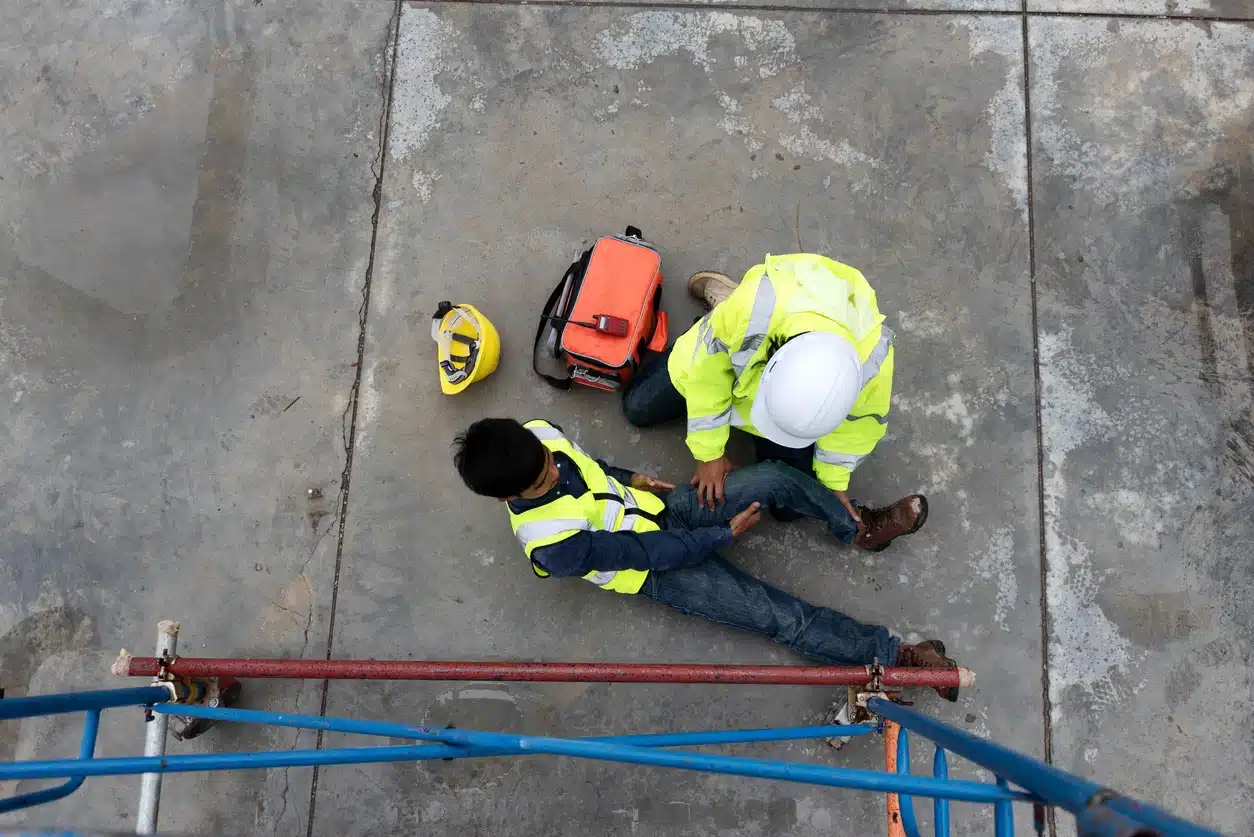
Construction workers face numerous risks on job sites, especially when safety protocols aren’t followed. Many of these risks can lead to serious injuries and even fatalities. For instance, in 2020, the number of nonfatal falls, slips, and trips was higher for construction workers than for all workers in other industries, according to the Bureau of Labor Statistics (BLS).
The specific types of job site risks that construction workers face may depend on the project. However, some dangers are more common than others. According to the Occupational Safety and Health Administration (OSHA), the leading causes of construction fatalities are falls, struck-by incidents, caught-between incidents, and electrocutions.
Understanding common construction accidents can help you and your team stay safe and avoid potential risks. Learn more about the biggest construction site risks, the causes of these risks, and how to reduce the risk of these dangers on the job.
Falls
Overview
In 2021, OSHA’s most frequently cited job site violation was falls. The agency issued more than 5,400 violations for falls during that year, which totaled a combined $28.8 million in penalties. The most common violation was failing to provide workers with adequate fall protection.
Causes of Falls
Falls are often caused by inadequate safety measures, such as the lack of guardrails, safety nets, or personal fall arrest systems. Other contributing factors include:
- Unstable Work Surfaces: Working on scaffolding, ladders, or roofs that are not properly secured.
- Environmental Hazards: Slippery or uneven surfaces, poor weather conditions, or obstructions.
- Human Factors: Lack of training, improper use of equipment, or negligence.
Prevention
Because over 62% of construction workers are exposed to heights, it’s essential to have the right personal protective equipment (PPE) on the job site. Using well-fitting and tethered safety harnesses can reduce the risk of a fall injury. OSHA also recommends using a guardrail system whenever possible.
- Training and Awareness: Regular training on fall prevention and proper use of equipment.
- Proper Equipment: Ensure all workers have access to and use appropriate fall protection gear.
- Regular Inspections: Routine checks of work surfaces and equipment to identify and address potential hazards.
Struck-By Incidents
Overview
Struck-by accidents are one of the biggest causes of construction job site fatalities. According to OSHA, a struck-by accident occurs when a construction worker comes into contact with a flying object, falling object, swinging object, or rolling object. Examples include a worker getting hit by a vehicle or a flying object, like a tool.
Causes of Struck-By Incidents
- Moving Equipment: Cranes, trucks, and other heavy machinery.
- Falling Objects: Tools, debris, or materials falling from heights.
- Swinging or Rotating Objects: Crane loads, swinging tools, or machinery parts.
Prevention
Struck-by accidents can result in fatalities, so it’s extremely important to reduce potential risk on the job site. Everyone on the job site should always wear proper head protection to avoid head trauma from a flying or falling object. When working at heights, it’s a good idea for workers to tether their tools to their belts to avoid falling tools.
- Protective Gear: Wearing hard hats and high-visibility clothing.
- Safe Equipment Operation: Proper training and adherence to safety protocols when operating machinery.
- Controlled Access Zones: Restricting access to areas where heavy equipment is in use.
Electrocution
Overview
Electrocution is one of OSHA’s big four construction hazards. Some of the biggest electrical hazards on job sites are faulty wiring, contact with live overhead power lines, improper use of extension cords, and contact with damaged equipment or power tools.
Causes of Electrocution
- Faulty Wiring: Exposed wires, improper installation, or damaged insulation.
- Contact with Power Lines: Accidental contact with overhead or underground power lines.
- Damaged Equipment: Using tools or machinery with frayed cords or broken plugs.
Prevention
Protecting workers against accidental electrocution is essential. To avoid this, job site managers should use an Assured Equipment Grounding Conductor Program (AEGCP), which is recommended by OSHA. Additionally, all cord sets, plugs, attachments, and power equipment should be inspected at the beginning of each workday. Avoid using cords that are frayed or have exposed wires.
- Regular Inspections: Daily checks of all electrical equipment and wiring.
- Proper Training: Educating workers on safe practices around electricity.
- Use of Ground Fault Circuit Interrupters (GFCIs): To protect against electrical shocks.
Caught-Between Incidents
Overview
Caught-between incidents happen when a worker sustains a crushing injury between objects. It’s another one of OSHA’s Focus Four hazards. This can happen when workers are pulled into machinery or are compressed between shifting, rolling, or sliding objects. Caught-between accidents can also be caused by cave-ins when working in trenches.
Causes of Caught-Between Incidents
- Machinery: Getting caught in moving parts or machinery.
- Shifting Materials: Compressed between moving or collapsing materials.
- Cave-Ins: Trench collapses or unstable excavation sites.
Prevention
Proper safety precautions can help prevent these incidents. For example, all construction workers should wear proper PPE, like high-visibility clothing, to make themselves more visible to other people on the site.
- Equipment Safety: Regular maintenance and proper use of machinery.
- Trench Safety: Using protective systems like trench boxes or shoring.
- Training: Educating workers on the risks and safety measures associated with caught-between hazards.
Trips and Slips
Overview
Trips and slips are the second most common construction site risk. In 2020, more than 31% of all construction laborer fatalities came from falls, slips, or trips. Depending on the job site, workers might accidentally trip over loose cords, slip on uneven surfaces or wet surfaces, or trip over obstacles, like building materials.
Causes of Trips and Slips
- Loose Cords: Unsecured cables and wires.
- Wet or Uneven Surfaces: Spills, rain, or poorly maintained walkways.
- Obstacles: Debris, tools, and building materials left in walkways.
Prevention
To reduce the risk of trips and slips, it’s important to keep the job site organized and ensure that walkways are clear and marked. If a surface is wet or uneven, use signage to alert workers. Corded tools should be put away when not in use, and work areas should be kept clear of debris and waste at all times.
- Housekeeping: Regularly cleaning and organizing the worksite.
- Signage: Using signs to warn of hazards like wet floors or uneven ground.
- Proper Lighting: Ensuring adequate lighting to identify potential tripping hazards.
Fire and Explosions
Overview
Fires and explosions on construction sites can be a major hazard to workers. Fires can be caused by a variety of things, like welding, poor maintenance of power tools, portable heating sources, generators, faulty wiring, and smoking. Using flammable or combustible materials can also contribute to fire and explosion risks.
Causes of Fires and Explosions
- Welding and Cutting: Sparks from welding and cutting operations.
- Faulty Equipment: Malfunctioning tools or generators.
- Flammable Materials: Improper storage or handling of flammable substances.
Prevention
To reduce fire risks, make sure to have multiple fire extinguishers easily accessible on the job site. All flammable materials should be safely stored when not in use. When doing heat work, have a manager supervise and make sure all tools cool down completely before they are put away, or before workers leave the job site for the day.
- Fire Extinguishers: Placing them strategically around the job site.
- Proper Storage: Safely storing flammable materials.
- Supervision: Having a responsible person oversee hot work operations.
Vehicles
Overview
Vehicles pose a significant threat to construction workers involved in road projects. OSHA found that the majority of fatalities that occur in road construction work zones are caused by a worker being hit by construction equipment or a car.
Causes of Vehicle Accidents
- Traffic: Moving vehicles in and around the construction zone.
- Heavy Equipment: Operating construction vehicles like bulldozers, dump trucks, and backhoes.
- Visibility Issues: Poor visibility due to weather conditions or worksite layout.
Prevention
When working on a road project, it’s important to follow all safety precautions. Depending on your location, your state’s Department of Transportation (DOT) may have its own rules and regulations around road work safety practices.
- Traffic Management Plans: Creating a plan to control vehicle movement around the site.
- High-Visibility Gear: Ensuring all workers wear high-visibility clothing.
- Designated Areas: Establishing specific areas for different activities, such as staging, storage, and parking.
Demolition
Overview
Demolition is necessary on many job sites, and it can lead to construction accidents. For example, demolishing unknown construction materials, including materials with hidden lead, asbestos, or other chemicals, could cause harm to workers. Unstable materials could also collapse and injure workers.
Causes of Demolition Accidents
- Hazardous Materials: Exposure to asbestos, lead, or other toxic substances.
- Structural Failures: Collapse of unstable structures during demolition.
- Explosives: Improper handling or detonation of explosives used in demolition.
Prevention
To prevent demolition accidents, it’s essential to complete an engineering survey to better understand the type of materials used in the structure, the condition of the structure, and the risk of a collapse. It’s also important to assess health hazards, like asbestos exposure.
- Engineering Surveys: Conducting thorough assessments before demolition.
- Hazardous Material Handling: Properly identifying and handling hazardous materials.
- Safety Protocols: Following strict safety guidelines during demolition activities.
Overexertion
Overview
Overexertion is a common workplace injury, especially in construction. Workers are often required to bend over, lift heavy objects, perform repetitive movements, and work in awkward positions that cause overuse injuries. This can lead to a variety of issues, like back problems, muscle strains, tendinitis, and rotator cuff tears.
Causes of Overexertion
- Heavy Lifting: Frequently lifting heavy materials or equipment.
- Repetitive Movements: Performing the same motion repeatedly over long periods.
- Awkward Postures: Working in positions that strain the body.
Prevention
OSHA maintains ergonomic standards that all workplaces should follow. However, creating an ergonomics program for your own construction company can also help educate workers on proper ergonomics and how to avoid overuse injuries.
- Ergonomics Training: Educating workers on proper lifting techniques and ergonomics.
- Use of Tools and Equipment: Using tools that reduce physical strain, such as motorized screeds or rebar-tying tools.
- Worksite Layout: Designing work areas to minimize the need for awkward postures and repetitive movements.
Ground Collapse
Overview
Ground collapse is a risk on many construction sites, particularly when workers are below ground. It can happen when a foundation is not strong enough to hold workers, or when wet soil erodes. Ground collapses can happen quickly and sometimes without any warning.
Causes of Ground Collapse
- Unstable Soil: Weak or eroded soil that cannot support the load.
- Improper Shoring: Lack of or inadequate trench support systems.
- Environmental Factors: Heavy rainfall or waterlogging that weakens the ground.
Prevention
To prevent ground collapse injuries, it’s important to evaluate all surfaces before starting work. This also includes dirt and soil that workers might be digging in. If workers are doing work in a trench, they should use a protective system to avoid getting stuck or buried.
- Soil Testing: Conducting thorough soil assessments before excavation.
- Protective Systems: Using trench boxes, shoring, or sloping to support trenches.
- Monitoring: Continuously monitoring the condition of the excavation site.
Cranes
Overview
Between 2011 and 2017, the Census of Fatal Occupational Injuries (CFOI) reported nearly 300 crane-related deaths. That’s an average of 42 crane fatalities per year over this period. Crane accidents can occur if the crane collapses, comes into contact with power lines, or a loaded crane hits someone on the ground.
Causes of Crane Accidents
- Mechanical Failures: Malfunctions or breakdowns in crane components.
- Power Line Contact: Cranes coming into contact with overhead power lines.
- Improper Use: Operating cranes beyond their capacity or in unsafe conditions.
Prevention
Any worker that is operating a crane should be properly trained and certified by a reputable organization, like the National Commission for the Certification of Crane Operators (NCCCO). Cranes should be inspected before use to avoid mechanical issues. Additionally, a trained individual should guide the crane operator on where to place loads, which can help avoid accidents.
- Training and Certification: Ensuring operators are properly trained and certified.
- Regular Inspections: Conducting routine checks of crane equipment.
- Guidance and Supervision: Having a designated spotter to assist with crane operations.
Forklifts
Overview
Forklift accidents are not uncommon. Between 2011 and 2017, there were more than 600 fatalities from forklift-related incidents. There were also about 7,000 nonfatal forklift-related injuries during this time that required workers to take time off work.
Causes of Forklift Accidents
- Operator Error: Lack of training or careless operation.
- Mechanical Issues: Malfunctions or poor maintenance of forklifts.
- Worksite Conditions: Slippery surfaces, narrow aisles, or cluttered environments.
Prevention
Forklift injury prevention starts with proper training. Operators should wear seat belts, use a spotter to back up when visibility is low, avoid sharp turns, drive slowly on slippery surfaces, and never drive with the forks up. Other workers on the ground should stay clear of forklifts while they are in operation.
- Training Programs: Providing comprehensive training for forklift operators.
- Safe Practices: Enforcing safety rules such as wearing seat belts and using spotters.
- Worksite Organization: Keeping aisles clear and maintaining safe driving conditions.
Chemical and Toxin Exposure
Overview
In 2020, almost 9% of all workplace fatalities were from construction workers who had been exposed to harmful substances or environments. It’s common for construction workers to get exposed to lead, asbestos, PVC, and heavy metals on job sites. Workers may also get sick from exposure to dust, silica, formaldehyde, and mold.
Causes of Chemical and Toxin Exposure
- Hazardous Materials: Presence of lead, asbestos, and other toxins in construction materials.
- Dust and Particulates: Inhalation of dust from cutting, grinding, or demolishing materials.
- Chemical Handling: Improper use or storage of chemicals.
Prevention
The best way to reduce the risk of chemical and toxin-related illnesses is to provide PPE to workers, like respiratory masks, gloves, and eye protection. Make sure to follow guidelines on the length of time that workers can be exposed to these chemicals before potential harm may occur. The NIOSH Pocket Guide to Chemical Hazards includes a comprehensive list of chemicals and toxins and the permissible exposure limits of each one.
- Personal Protective Equipment (PPE): Providing appropriate respiratory, eye, and skin protection.
- Exposure Limits: Adhering to recommended exposure limits and guidelines.
- Safe Practices: Implementing procedures for safe handling and disposal of hazardous materials.
Simplifying Safety in Construction
Encouraging a Culture of Safety
One of the best ways to stay safe on job sites and reduce the risk of construction accidents is by encouraging a culture of safety, conducting proactive safety stand-downs if risks appear on the jobsite, and making safety procedures easy to follow.
Training and Documentation
You should also train workers consistently, particularly when safety standards are changed or updated. It’s a good idea to appoint one individual, such as a Safety Manager or Safety Director, in your company to oversee safety practices, train workers, report injuries, and enforce compliance.
Additionally, it’s a good idea to document all safety incidents that arise, even if no one gets hurt. Construction software enables construction workers to keep documents like incident reports, site plans, and daily logs in one place. This gives project stakeholders access to common sources of risk or potential hazards on the jobsite and works together to make construction sites safer.
Contact Us
If you or a loved one have been injured in an accident, whether at work or elsewhere, contact us to handle your personal injury and workers’ compensation claims.